Ok last year finally decided that it was time to convert the shed so that I could put a few extra pins in it. Single block built with leaking roof so plan was to fully insulate it and re-roof with either anti condense or insulated roof sheets.
Started well as removed the concrete tiles, roof spars, doors, windows and knocked the front wall down.
As it was only single block have replaced the front wall with double block insulated and fitted dg french doors and window.
All new wood for roof (£££££££££), joiner decided that rather than spars over the blocks, back to front, he would hang it down from the blocks and build a framework for the roof/support with a pan back and front and the sheets on top.
Everything had gone ok up to this point but tbh I wasn't sure about the construction of the roof/frame however thought it would be ok once sheeting was fitted, wrong!!
I told the builder that I wanted insulated roof sheets/anti condense so that there wouldn't be any condensation but as he didn't know a lot about roof sheets he left it to the joiner to organise.
Nice sheets supplied but unfortunately no anti condense strip or insulation on them so of course next morning, after fitting, drip, drip, drip - could nearly have an effing shower in there.
The plan was always to put extra insulation between the roof framework and then board/plaster but didn't solve the condensation, probably made it worse as no air flow/vents.
So job stopped, lots of expensive kingspan falls down daily and no solution yet.
The builder has agreed that the roof panels need to come off and be replaced so my question is to any roofers, tradesperson, excellent diyer's on here. What/how is the best way to rectify/sort this?
Original build
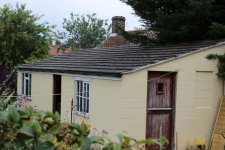
Roof, doors, windows removed
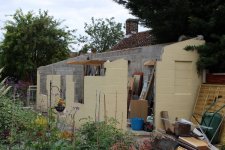
Wall removed
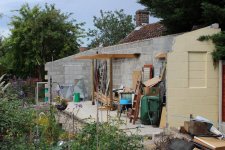
Wall removed
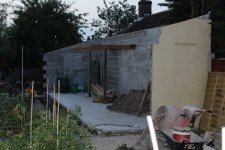
Front wall, dg and roof fitted
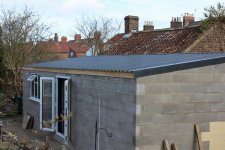
Condensation, insulation, etc
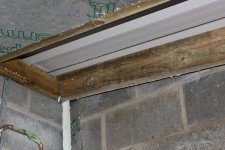
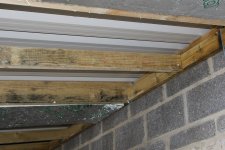
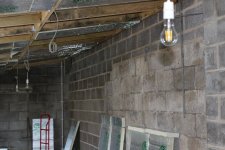
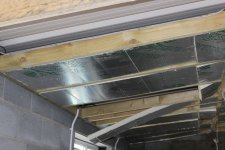
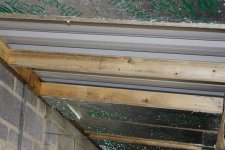
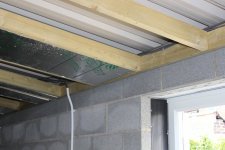
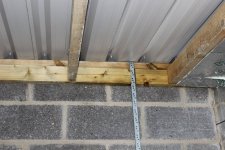
Started well as removed the concrete tiles, roof spars, doors, windows and knocked the front wall down.
As it was only single block have replaced the front wall with double block insulated and fitted dg french doors and window.
All new wood for roof (£££££££££), joiner decided that rather than spars over the blocks, back to front, he would hang it down from the blocks and build a framework for the roof/support with a pan back and front and the sheets on top.
Everything had gone ok up to this point but tbh I wasn't sure about the construction of the roof/frame however thought it would be ok once sheeting was fitted, wrong!!
I told the builder that I wanted insulated roof sheets/anti condense so that there wouldn't be any condensation but as he didn't know a lot about roof sheets he left it to the joiner to organise.
Nice sheets supplied but unfortunately no anti condense strip or insulation on them so of course next morning, after fitting, drip, drip, drip - could nearly have an effing shower in there.
The plan was always to put extra insulation between the roof framework and then board/plaster but didn't solve the condensation, probably made it worse as no air flow/vents.
So job stopped, lots of expensive kingspan falls down daily and no solution yet.
The builder has agreed that the roof panels need to come off and be replaced so my question is to any roofers, tradesperson, excellent diyer's on here. What/how is the best way to rectify/sort this?
Original build
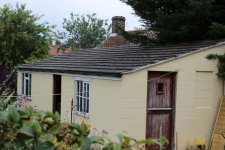
Roof, doors, windows removed
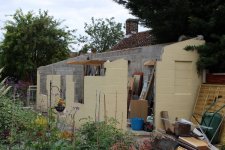
Wall removed
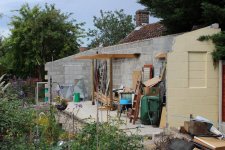
Wall removed
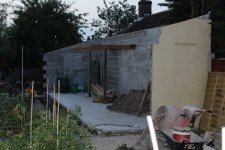
Front wall, dg and roof fitted
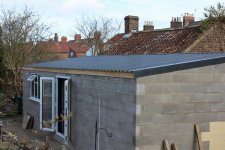
Condensation, insulation, etc
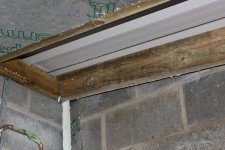
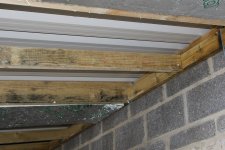
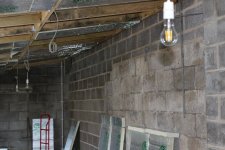
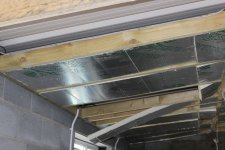
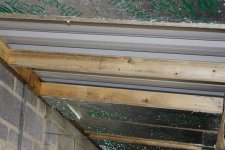
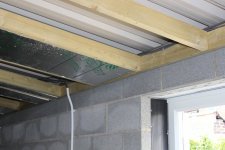
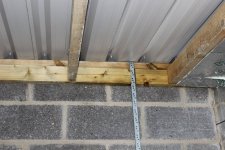