While waiting for the plastics to arrive I decided to proceed with some other tasks. First up was repairing the volcano. I found a great guide online and followed the procedure. First up, pack out the volcano hole with tin foil:
Next, mix up some clear silicone with some orange paint and apply it to the damaged area, use a paint brush to create the desired look. The clear silicone will show light through just like other areas of the volcano:
Next, I waited for the silicone to dry (I left it 24 hours) and then removed the foil from the inside. Finally I mixed some paint in order to re-create the grey finish to the repaired area:
and there we have it, one repaired volcano!
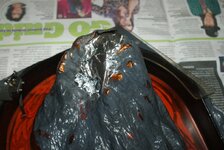
Next, mix up some clear silicone with some orange paint and apply it to the damaged area, use a paint brush to create the desired look. The clear silicone will show light through just like other areas of the volcano:
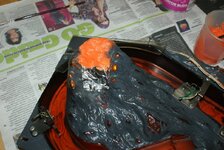
Next, I waited for the silicone to dry (I left it 24 hours) and then removed the foil from the inside. Finally I mixed some paint in order to re-create the grey finish to the repaired area:
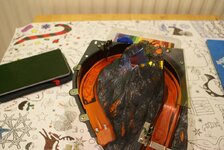
and there we have it, one repaired volcano!