Hi all,
It's been awhile since I have visited this forum so I thought it was time to give a brief update on things from Shenzhen. I have built the pinball factory from an empty building and that was no mean feat. It involved first finding a suitable place then hiring staff and fitting the place out with tools, machinery etc. Then I had staff sitting around with very little to do so I decided to make a fairly simple product initially (compared to a pinball machine) and that's how the Hankin licenced video game tables project was born.
Building these tables has allowed me to train up the staff (who are already qualified welders, cabinet makers, a fitter & turner etc) to the quality levels I expect and, more importantly, my customers expect! We have shipped out six containers of these tables to date and, as you can see from the pictures attached, we have another container built and ready to ship. The tables are being greeted with rave reviews by all buyers I'm proud to say and we have had very few problems with them.
During the time we have been making these tables there have been several design staff working on mechanical parts and PCB design and layout for our pinballs. There are several machines in the works but the first will of course be Thunderbirds (based on the original series NOT the latest release). I am not going to say much about the other machines except that some are unlicenced themes.
I have been asked about pricing dozens of times and be be honest it is next to impossible for me to work out even a close estimation. The setup costs here have been astronomical and we are still a few months off from completing all of the bits we need. At that point I might have a better idea. For some examples of costs the die to stamp pinball legs was AU$5500 and for the top part of the lockdown bar (not including the internal metal parts) was AU$4600 - you can extrapolate that across the entire range of parts right down to switch leaves and insulators. Of course these are mostly one off costs but they still have to be paid up front for us to commence production. Add to that the complexities of ensuring every single part complies with RoHS requirements and it is a massive task.
We need to make all parts ourselves, in house, for a few reasons. First reason is that it is complex and expensive to import anything into China. Next is to guarantee the high quality that I demand we need to control things ourselves and also I never want to be placed in a position where I am held to ransom by a supplier. We also have our own woodshop with CNC machine etc so we manufacture all of our own cabinets as well. Very little is done by outside suppliers with some exceptions like winding the mains transformers.
We are still on track for a 2015 release of Thunderbirds but time will tell how we go as there are still many things to complete. My job at the factory is to get all the parts designed and made NOT to concentrate on the nitty gritty of the design details of each machine. That is being done by smarter people than me but it is all coming together - probably a little better than I expected.
Some pictures below show a few of the pinball parts that have been made up and are in stock and some areas of the factory, mainly the line for assembling the Hankin tables. Building these has helped with cash flow as well as being a great training tool for the staff. The upstairs sections of the factory (not shown in the pictures) is devoted to CAD design of the various parts and construction of smaller assemblies.
Those who want to follow our progress can see updates when I am able to post them (Facebook is blocked in China) here:
facebook.com/HomepinPinball
Cheers,
Mike
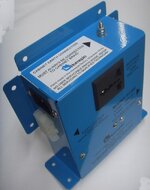